Engineered Lumber vs. Traditional Wood: Which Is Better for Your Build?
When it comes to framing, floor systems, and structural support, few choices matter more than the lumber you select. For years, the default option was simple: traditional dimensional lumber cut straight from the mill. But in recent decades, engineered lumber has become a go-to alternative for builders seeking performance, consistency, and strength.
So which is better for your next build—engineered or traditional? Like most decisions in construction, the answer depends on your goals, timeline, budget, and scope. At ProPonents, we supply both—and we help clients make the smartest choice based on the real needs of their project, not just price or popularity.
In this post, we’ll break down the key differences between engineered lumber and traditional wood, where each performs best, and what you should consider when choosing one over the other.
Understanding the Basics
Let’s start with a quick definition.
Traditional wood, or solid-sawn lumber, is what most people think of when they picture framing materials—dimensional boards like 2x4s, 2x10s, and 4x6s, cut directly from logs. It’s been used for centuries, is readily available, and remains popular across residential and light commercial construction.
Engineered lumber, on the other hand, is manufactured. It’s made by binding layers of wood fibers, veneers, or strands together using adhesives and pressure to create a product that’s stronger, straighter, and more dimensionally stable than traditional wood. Common types include LVL (Laminated Veneer Lumber), LSL (Laminated Strand Lumber), PSL (Parallel Strand Lumber), and I-joists.
Engineered lumber is designed to solve problems that traditional wood can’t always handle—especially in large-scale, long-span, or complex projects.
Strength and Stability: Engineered Wood Takes the Lead
One of the most significant benefits of engineered lumber is its predictable performance. Because it's manufactured under controlled conditions, engineered products are:
- Less prone to warping, twisting, or bowing
- More uniform in strength and dimensions
- Ideal for long spans without sagging or deflection
That means if you're building wide-open spaces, like in multifamily developments or modern residential designs with large rooms and minimal supports, engineered lumber gives you more design flexibility and fewer callbacks due to shifting or settling.
By contrast, traditional lumber is a natural material, and even the highest-grade boards are subject to the quirks of nature—knots, moisture content, grain direction, and environmental response. It can perform beautifully, especially in smaller spans or non-load-bearing walls, but it’s rarely as consistent.
Cost Considerations: Short-Term vs. Long-Term Value
Here’s where the debate gets more nuanced. Traditional wood is often less expensive up front, making it a preferred option for budget-sensitive builds or projects with straightforward framing needs.
But engineered lumber, while more costly per board, can offer value in other ways:
- Faster, more accurate installation due to uniform sizing
- Fewer material defects and waste
- Reduced need for mid-span supports or structural modifications
- Fewer long-term issues related to movement or shrinkage
So while you may spend more on materials, you may also spend less on labor, corrections, and engineering accommodations. That’s the calculation savvy builders make when comparing the two.
At ProPonents, we regularly walk through these comparisons with clients to help clarify where it makes sense to invest and where you can trim costs without risk.
Build Type Matters
Not all projects demand the same performance out of their materials. Here’s a general guide based on the types of builds we commonly support:
Traditional Lumber Is Often Ideal For:
- Single-family homes with standard spans and conventional layouts
- Load-bearing and non-load-bearing interior walls
- Exterior walls in low-rise builds
- Budget-conscious renovations or spec homes
Engineered Lumber Shines In:
- Multifamily housing or large residential structures
- Open floor plans with wide spans
- Mid-rise buildings with structural complexity
- Areas where minimizing deflection or bounce is critical (e.g., floor joists)
Again, there’s no one-size-fits-all. But knowing where each material excels is key to making the best call for your specific project.
Sourcing and Lead Times in 2025
One thing to consider in today’s market is availability. With global supply chains still adjusting and regional demand fluctuating, engineered lumber can sometimes come with longer lead times depending on the product and location.
At ProPonents, we’ve built strong supplier relationships that allow us to keep both traditional and engineered products in stock or secure them quickly when demand spikes. We’ll also flag any upcoming shortages we see on the horizon, so you’re not caught off guard mid-project.
If you’re weighing the two options and your build is time-sensitive, let us help you strategize. We might suggest a hybrid approach—engineered floor joists with dimensional studs, for example—to balance performance and availability.
So, Which Should You Choose?
The answer, of course, is: It depends—on your budget, your layout, your performance needs, and your timeline.
But the good news is you don’t have to figure it out alone.
At ProPonents, we don’t just supply lumber. We help builders make smart material decisions that support their design goals, protect their margins, and keep their projects moving forward.
Whether you're framing a single house or an entire development, we’ll walk you through your options, provide detailed pricing comparisons, and help you plan for every phase of your build.
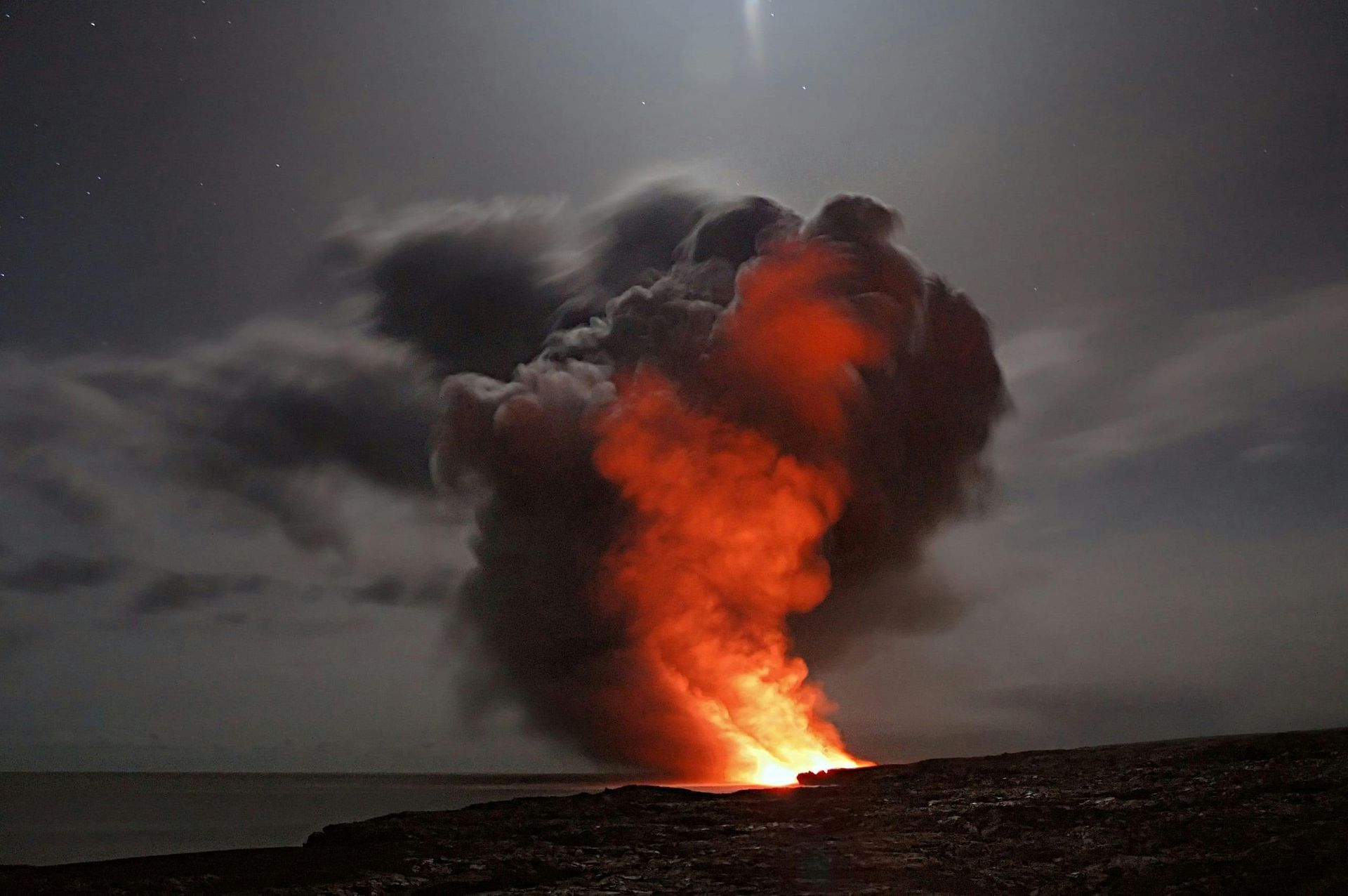
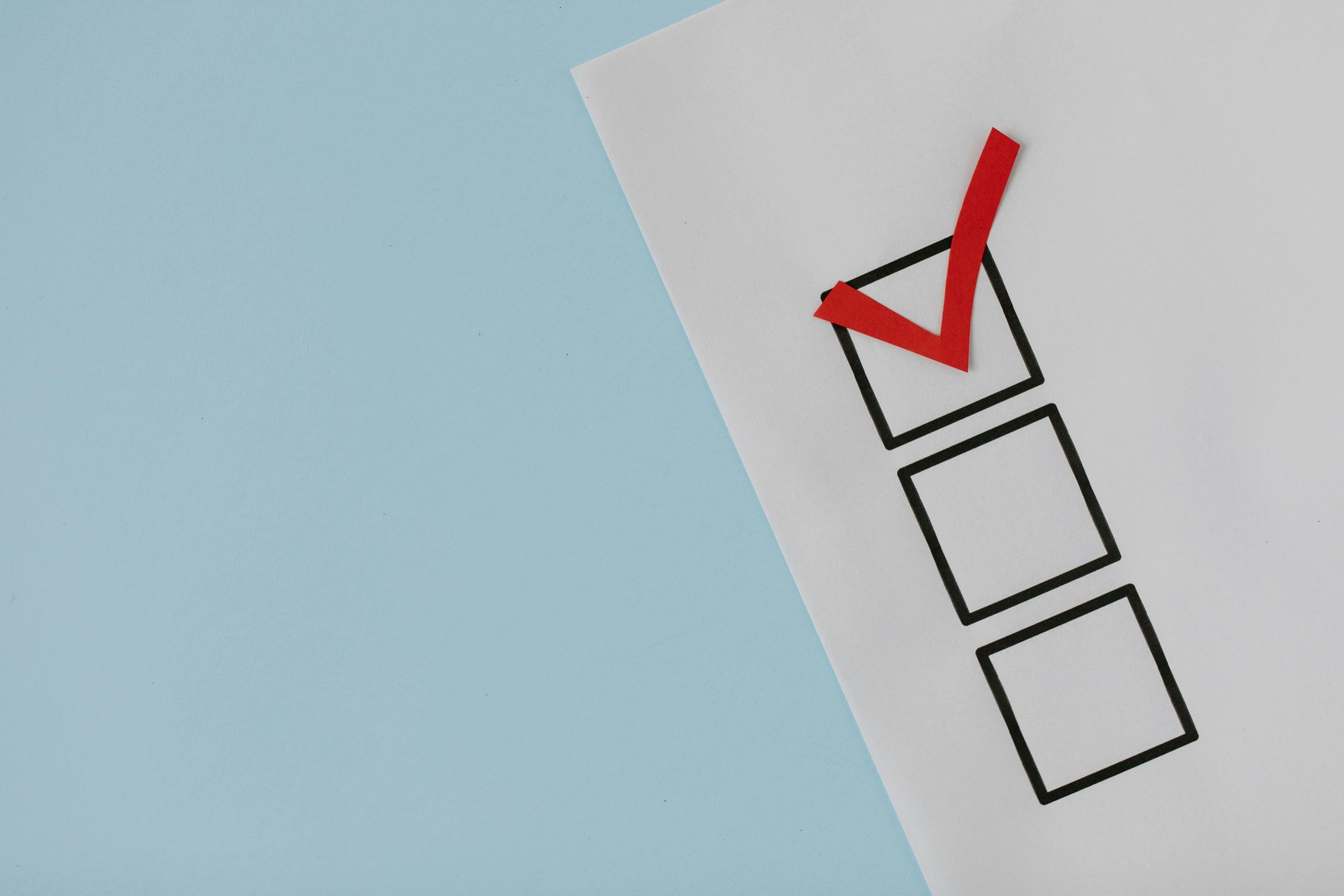
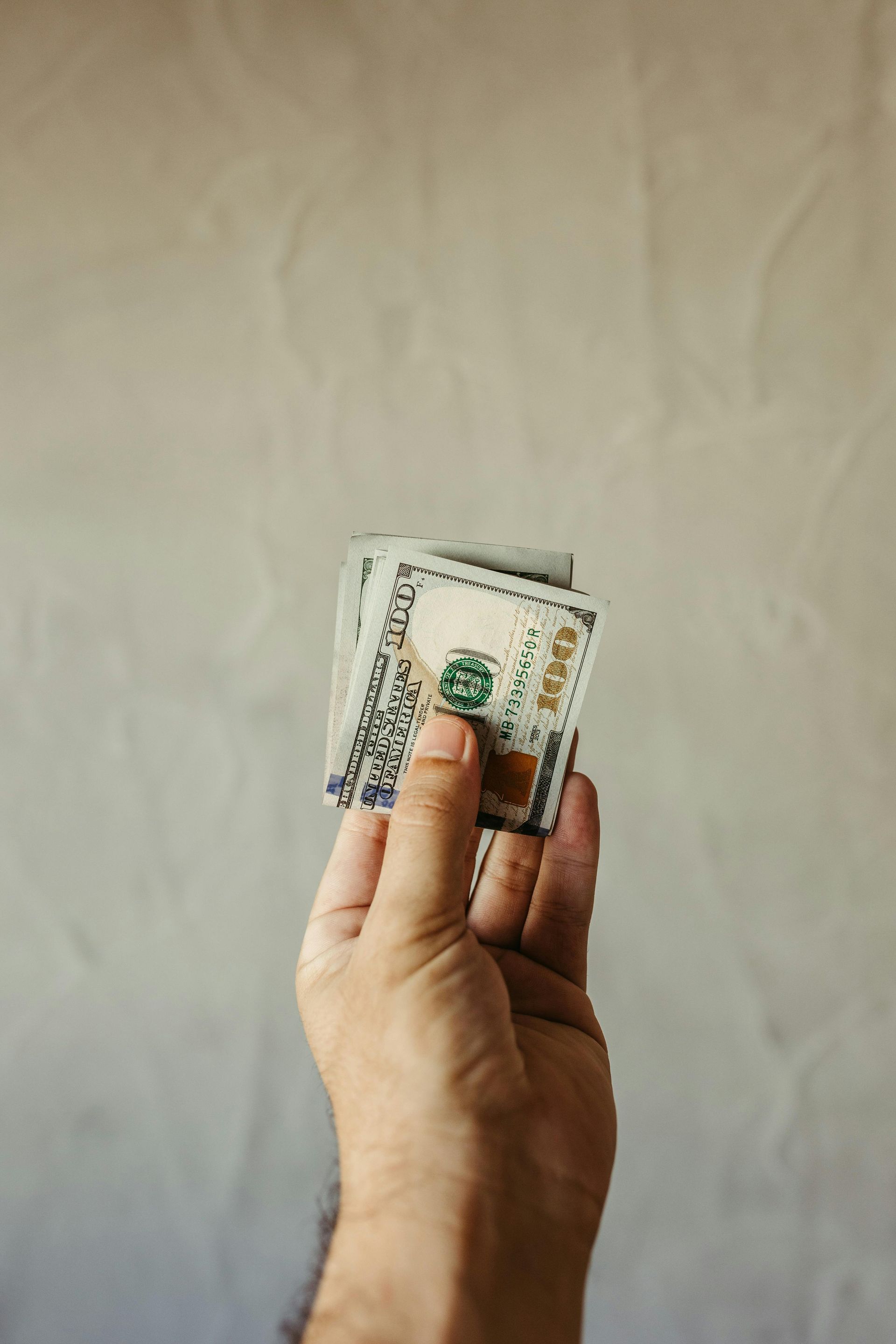
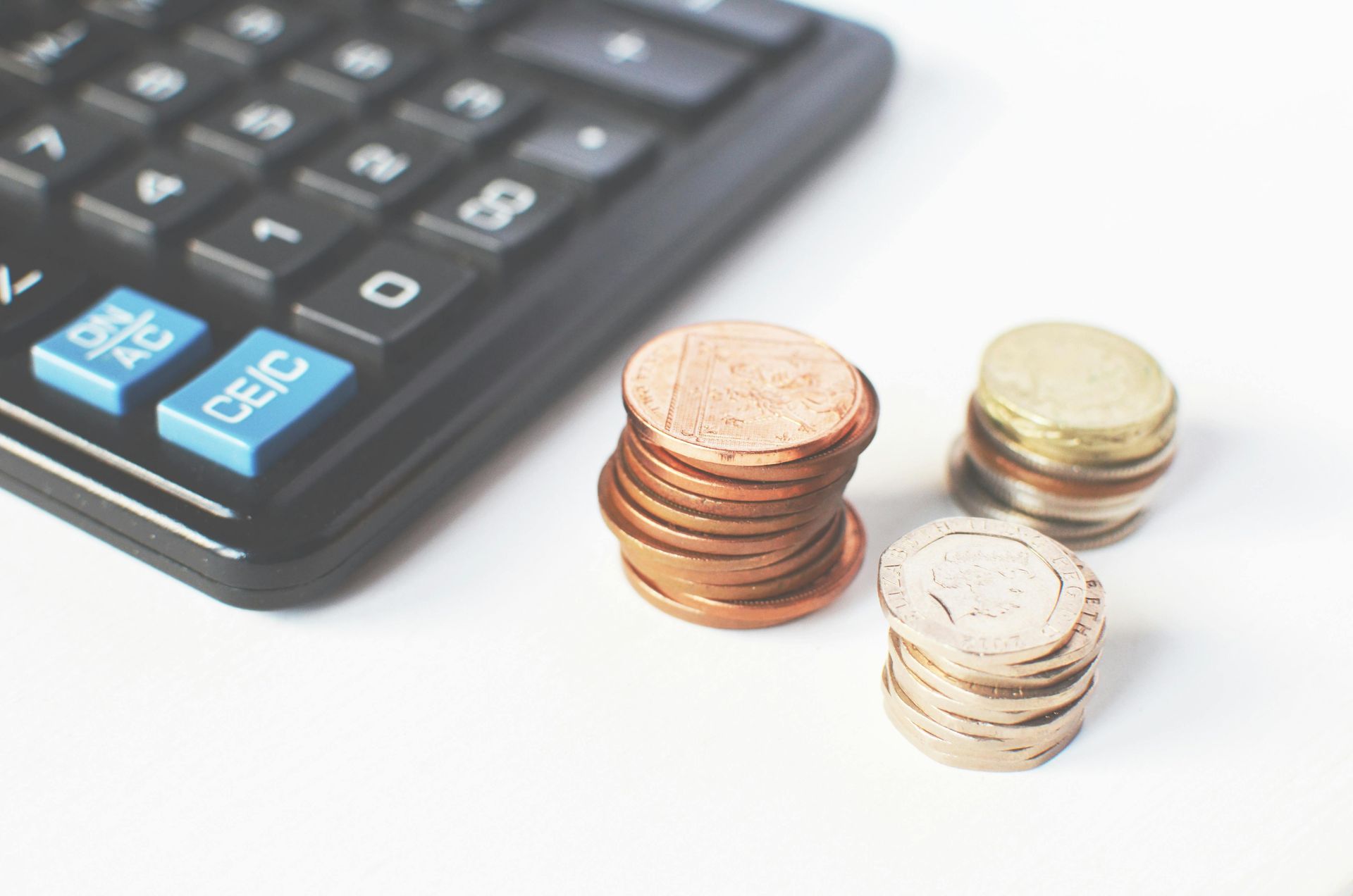
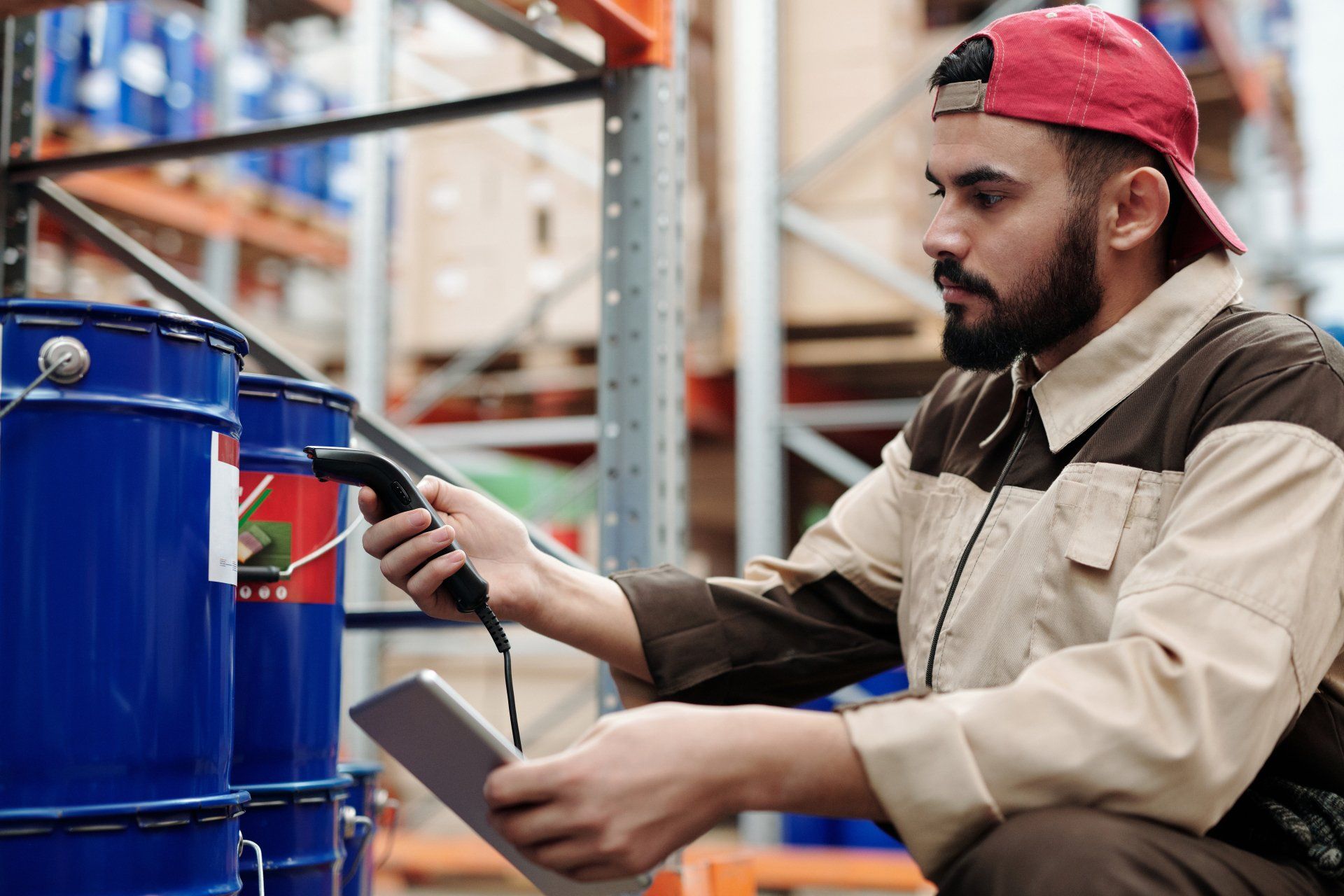
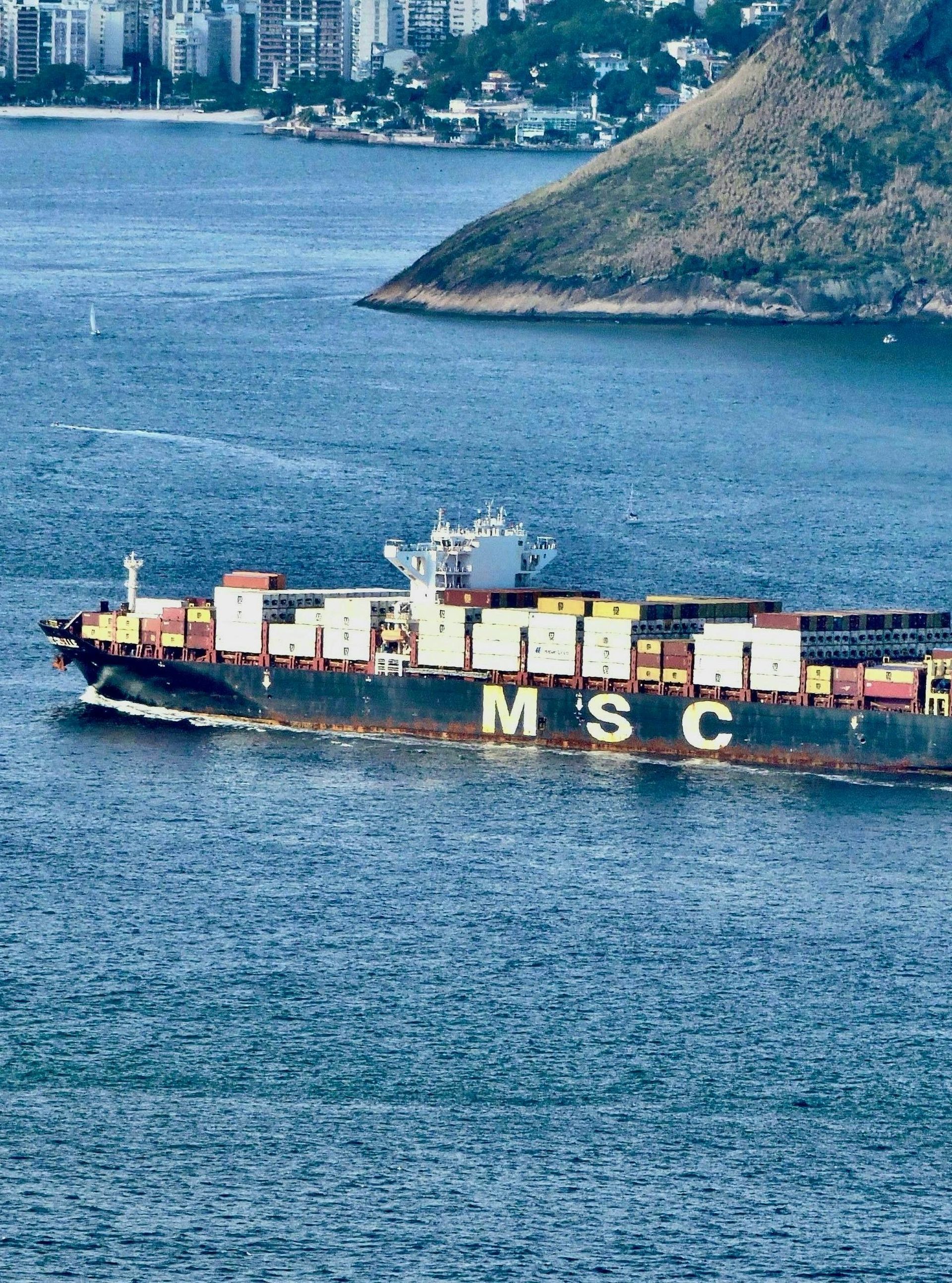
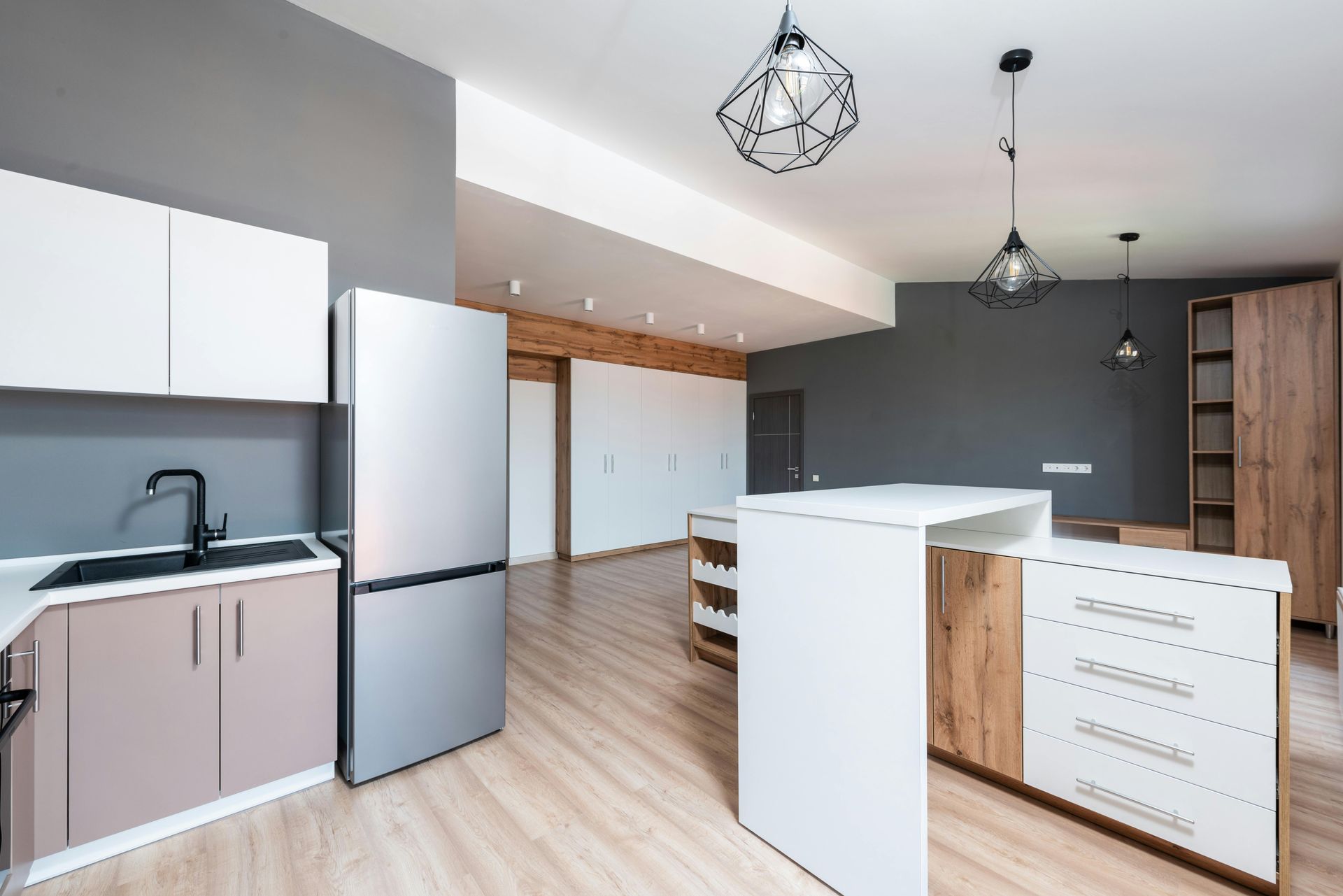
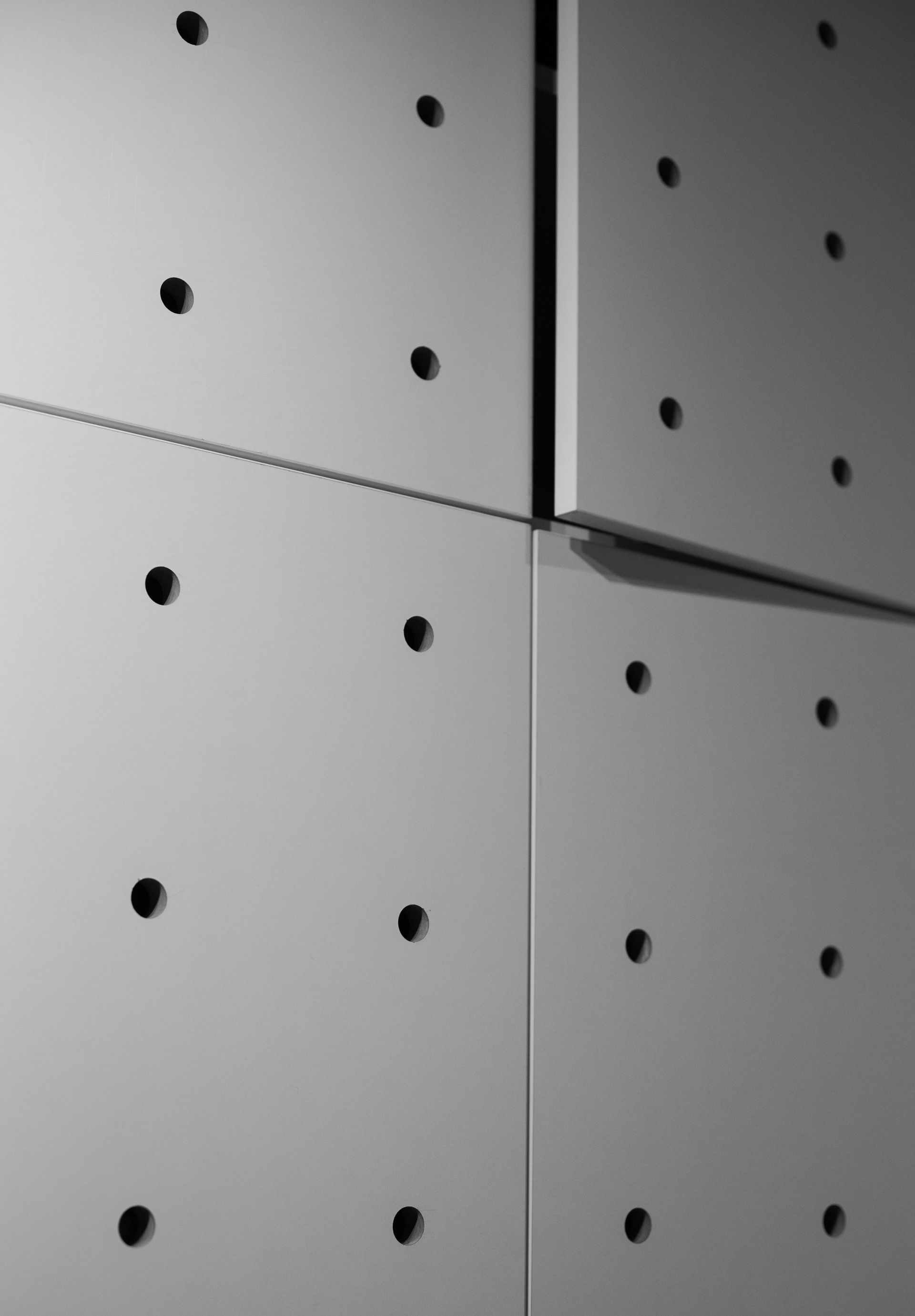
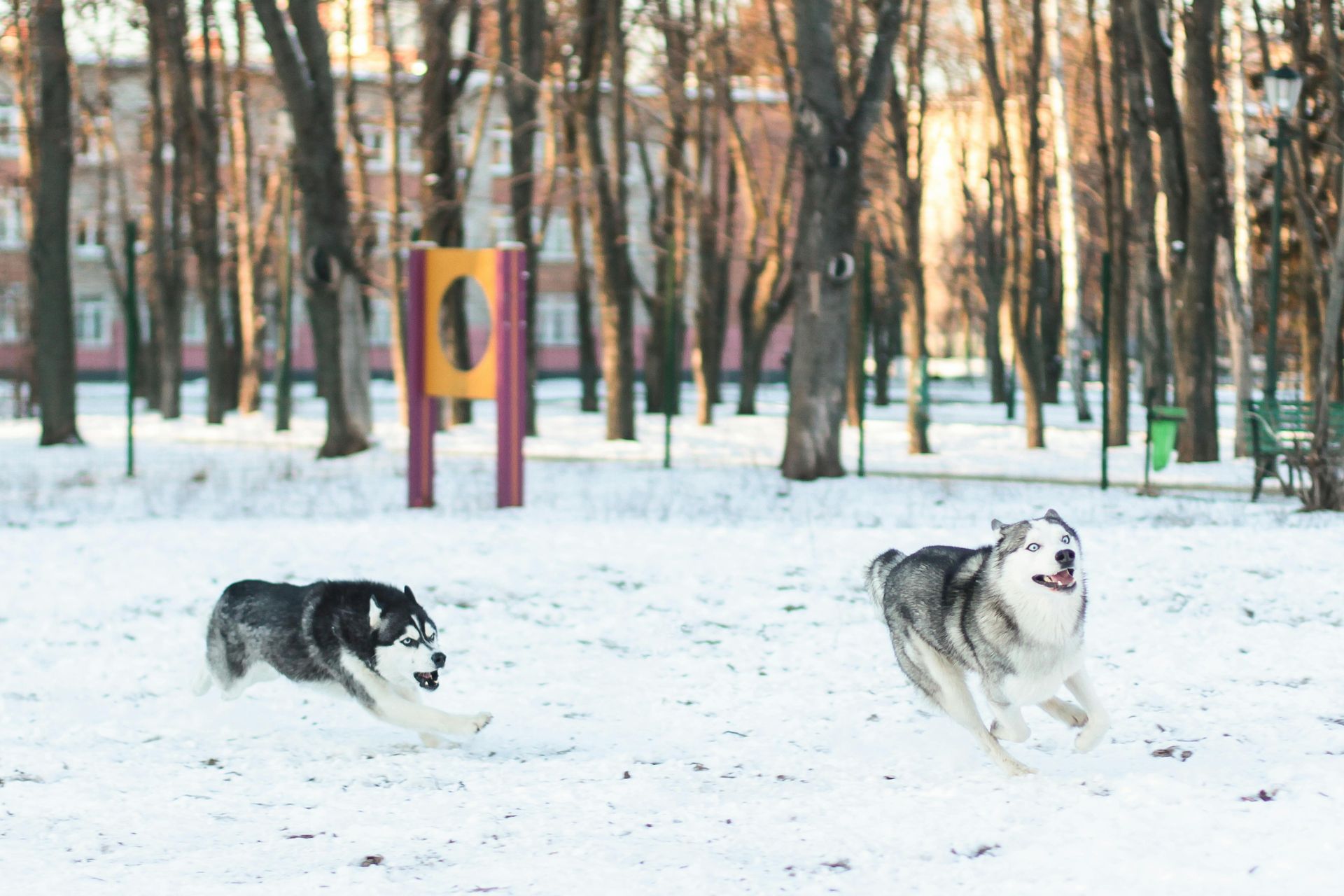
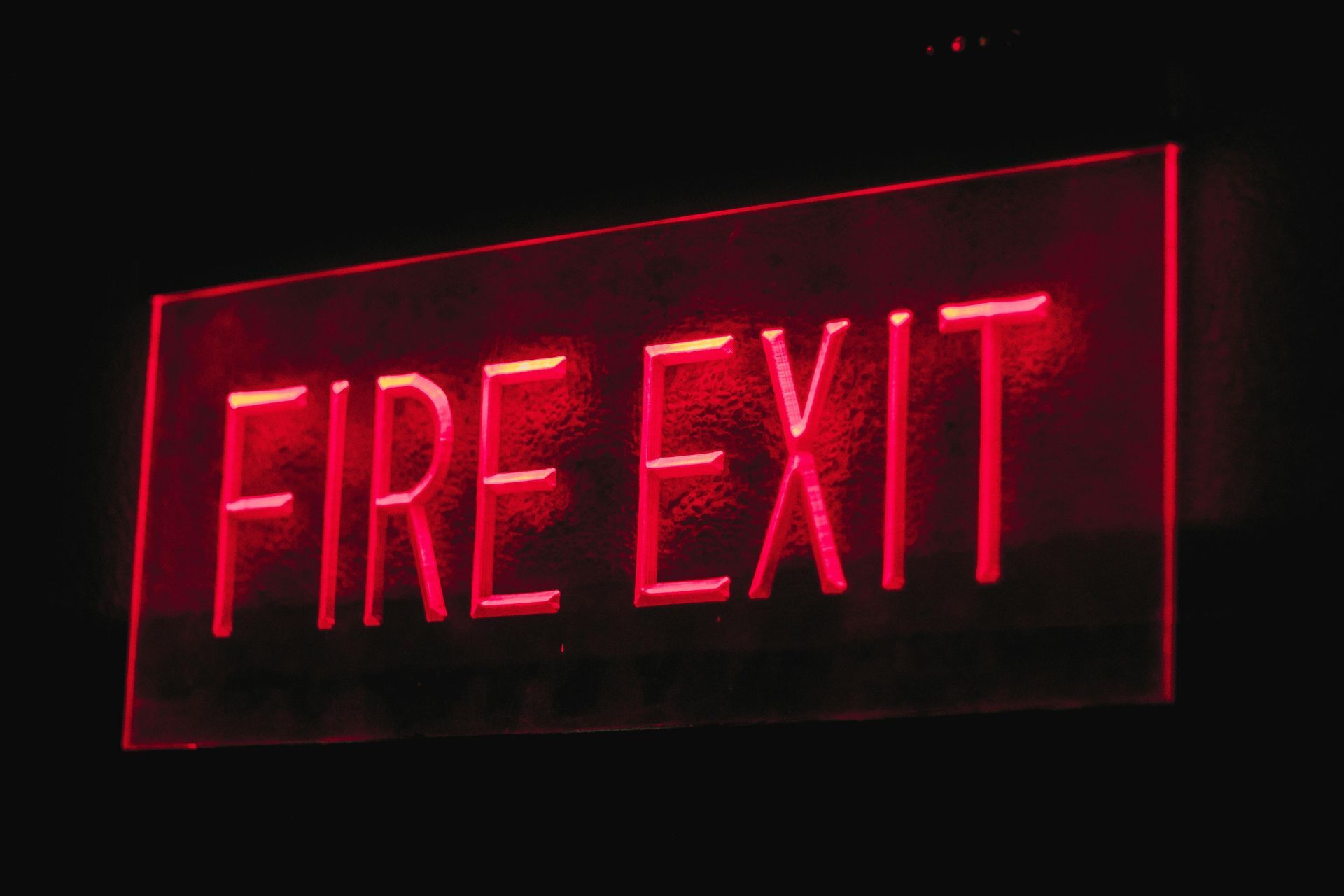